· announcement · 10 min read
Inaugural AMMO NYC 3-Day Masterclass a Success!
We learned so much from Larry Kosilla, Jason Rose, and Kevin Brown who shared their vast expertise and experience.
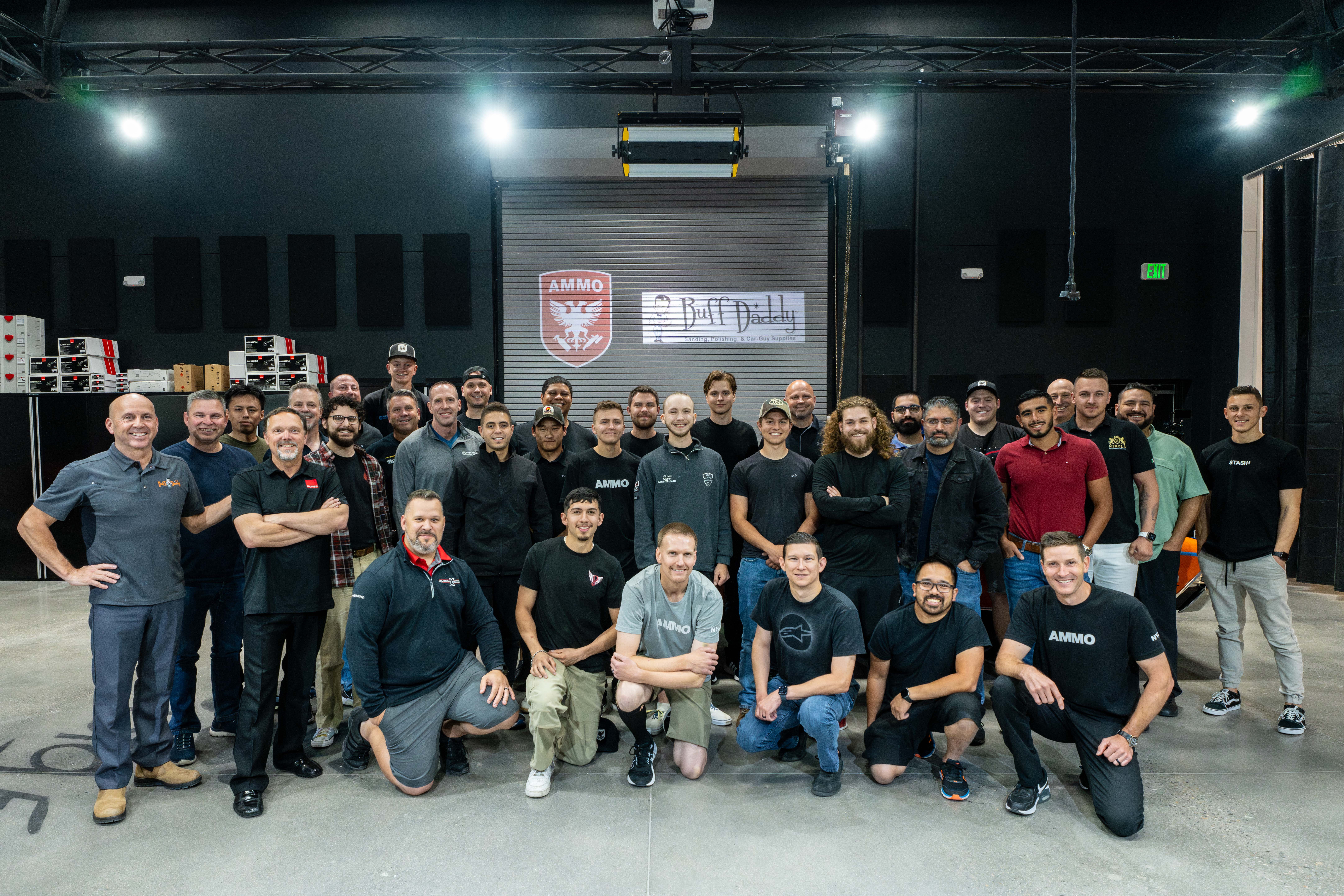
Overview
We spent an amazing three days with arguably the best folks in the detailing world; Larry Kosilla, Jason Rose, and Kevin Brown. The training was held at RUPES USA headquarters in Louisville, Colorado, where we covered so many topics and had our numerous questions answered at the RUPES Bigfoot Detailing Academy.
If any of the names mentioned aren’t familiar to you, continue reading to learn more about them and what they’ve accomplished in the detailing world.
Larry Kosilla
Larry Kosilla is the founder of AMMO NYC, a renowned brand in the automotive detailing industry. Through his YouTube channel, website, and social media platforms, Kosilla shares his extensive knowledge and passion for car care, detailing techniques, and product reviews. He is celebrated for his meticulous attention to detail and his ability to transform vehicles to showroom quality. Kosilla’s expertise has garnered a large and dedicated following, making him a trusted source of information and inspiration for car enthusiasts and detailing professionals worldwide. Additionally, he has developed a line of premium car care products under the AMMO NYC brand, further solidifying his reputation as a leading authority in the field.
Jason Rose
Jason Rose is a highly respected figure in the automotive industry, particularly in the realm of paint correction and polishing. He serves as the Global Director of Training for RUPES, a leading manufacturer of high-quality car detailing equipment and tools. With years of experience and expertise, Rose is known for his deep understanding of paint systems and his ability to develop innovative solutions for achieving flawless finishes on vehicles. He travels extensively to conduct training sessions and workshops, educating professionals and enthusiasts alike on the intricacies of paint correction and polishing techniques. Rose’s contributions to the field have earned him widespread recognition and respect, making him a trusted authority in the world of automotive surface care.
Kevin Brown
Kevin Brown, famously known as Buff Daddy, is a prominent figure in the world of car detailing and automotive care. He gained recognition through his presence on Autopia and other detailing forums where he shared his paper on the Kevin Brown Method which thoroughly explains his advanced paint correction techniques, a name that was coined after him by Todd Helme, a well known detailer. Brown is highly regarded for his meticulous approach to car care and his ability to achieve flawless results. His passion for detailing and dedication to providing valuable content has earned him a loyal following within the automotive community.
Our Three Days
Day 1
We started Day 1 with everyone arriving early and surprisingly, no one showing up late (as far as we could remember). We were all so eager to be at RUPES USA headquarters, ready to learn so much over the next three days. With the diverse range of skills and experience amongst the training attendees, we started the day by reviewing the most fundamental detailing basics to build a solid baseline. Some of those basics included the concept of residue control and how to manage it. We discussed in great depth about the elasticity of paint and other behavioral characteristics when being manipulated by different interfacing materials and techniques. After a few hours of reviewing and learning concepts in the training room, we eventually moved on to the more practical, hands-on side.
Before we stepped into the Bigfoot Training Academy garage where we were greeted by several test panels and a couple test vehicles (one was an attendee’s rental), Jason Rose demonstrated core concepts of paint correction such as understanding the surface and the potential approaches to restoring a vehicle’s paint surface. We learned about the differences between typical film disc sanding versus foam disc sanding where the method of leveling the paint is much different. We were able to apply that learning by sanding with film abrasives as well as foam abrasives, the latter of which was a new technique to us. The foam abrasive that we used was introduced to us as the RUPES X-Cut which is a new foam abrasive that really impressed us and has been incorporated into our paint preservation workflow. As a follow-up to help reinforce these concepts and exercises, Rose highly recommended viewing a video titled, 10 Polishing Variables, in which he does an excellent job of explaining the variables involved when apporaching paint correction.
Towards the end of our first day, Kosilla walked us through some of the materials in his AMMO ATA 300 Professional Detail Training Course where we learned about finances, the balance sheet, PNL (Profit and Loss), cash flow, and how to use all of those tools effectively.
Day 2
For Day 2, Kosilla started the morning by going over hypothetical disaster scenarios with potential clients. He emphasized to always have a plan for any problematic scenarios. He encouraged everyone to explore and establish a good relationship with a local body and wheel shop so that when a problem arises, we’re able to immediately address any concerns by presenting the problem and the solution to the client at the same time. When communicating this to the client, the assumption there is we’ve already made arrangements for addressing the situation and it’s currently in progress. This high level of preparedness demonstrates a dedication to an amazing client experience despite the circumstances.
Kosilla introduced the Pareto principle which many of us were not familiar with. It was a very popular topic among our group and a new way of thinking for many. This is a technique that Kosilla has evolved and fine tuned over the years to curate the ideal clientele for him and the business which translates to him only having six core clients. His philosophy to impress upon us is that we should really strive to “want better, not more clients.”
After Kosilla’s talk, Rose welcomed us further into RUPES USA headquarters where we had the privilege to check out the team assembling the RUPES polishers. Prior to the arrival of RUPES to the United States, doing a full paint correction on a vehicle used to easily span multiple days using a combination of the rotary and dual-action polishers. Now with today’s modern polishers such as the RUPES Bigfoot LHR21 Mark III or the LHR15 Mark III, a full paint correction in the hands of a skilled technician can be achieved in as short as half a day. Coincidentally, the AMMO edition RUPES polishers were being assembled so we were definitely in for a treat. We had the opportunity to chat with Kyle Colwell, Operations Manager, and ask detailed questions about the assembly process, the time to assemble one unit, how many units are assembled in a day, and the warranty process. It really gave us that true behind-the-scenes experience that none of us were really expecting to get.
Upon returning to the training room from our behind-the-scenes tour, Kosilla continued discussing his approach to filtering clients. His approach to answering phone calls is with “Hello, this is Larry at AMMO. Is this for a movie, photo shoot, or an auction?” It’s a unique approach that really gave us that light-bulb moment and is something that we’ve implemented in the Concours tier of our Pricing page.
While we don’t exactly remember who originally suggested it (we believe it was Rose), someone suggested doing a step-down panel, any panel on a client’s vehicle where the stages of paint correction are visually demonstrated to educate and enforce the technician’s skill and expertise. Additionally, it was suggested that an improvement would be for a detailing business to have a sample hood with a step-down panel always on dispaly so that it’s immediately apparent to potential clients on what they can expect.
Day 3
On our third and final day, Kosilla went over business positioning strategies. We touched on five of these strategies which include customer service, price, convenience, differentiation, and quality. Within those five business positioning strategies, Kosilla suggested that we, as business owners, focus on one of these positioning strategies. While many of us would like to think we can focus on all five, Devil Pad’s primary focus has always been on quality followed by differentiation, customer service, convenience, and price, since our humble beginnings in 2008.
Later on in the day, we had the opportunity to jump on a live call with Thomas Palancia, International Division Manager, Detail Operations and Training Manager at Simoniz USA Inc. He shared his expertise from the chemical side of things and discussed the importance of understanding the pH Scale, how we use it in our daily lives, and how we leverage our knowledge of it to tackle the difficult challenges we encounter when detailing vehicles, both the interior and the exterior. In addition, we discussed the Occupational Safety and Health Administration (OSHA) Bloodborne Pathogens Standard as well as reviewed the Safety Data Sheet (SDS) and the contents within for detailing chemical products.
Towards the end of the day, Rose went over machine maintenance, particularly with RUPES polishers (obviously =P). He suggested that we apply dielectric lubricant or white lithium grease to the area between the backing plate and the rubber shroud. We should also be considerate with the base of the unit where the power cord exits and regularly vacuum the vents of any polish dust or other residue. A great video that covers these maintenance tips in greater detail can be viewed here from the RUPES YouTube channel.
To conclude our training, a very warm thank you and appreciation was shared by Kosilla, Rose, and Brown. As attendees to this inaugural training, we were very privileged to have three of the best in the industry to share their expertise and experiences. We were able to benefit by not only taking our paint correction to the next level but also really understand how to grow and evolve a detailing business more effectively and efficiently.
We’re AMMO Training Academy Certified
At the conclusion of the third day, we were presented with our official AMMO Training Academy certificates signed by Jason Rose, Larry Kosilla, and Kevin Brown. We are so thankful to have had the opportunity to earn this certificate and are proud to share and display it.
Additional SWAG We Received
In addition to the AMMO Training Academy certificate, we also received signed, personal photos that we took with Larry, Jason, and Kevin on Day 1 that were presented to us with our AMMO Training Academy certificates. As part of our attendance, we were also given a RUPES bag (not pictured), a token to the RUPES claw machine (how we got our RUPES cap), an AMMO Scangrip light, a bottle of AMMO X-Foliate, AMMO/RUPES stickers, a RUPES water bottle, and a personalized AMMO card signed by Larry.
Summary
The inaugural AMMO NYC 3-Day Masterclass was such a fun and amazing experience. We had the privilege of learning and hanging out with Larry, Jason, and Kevin. In addition, we received excellent assistance from other RUPES USA staff such as Sarah Coleman-Lienhart, Robyn Sweet, and AMMO’s newest addition, Brodie Kellett aka “Aussie Larry.”
We sincerely hope that future training sessions will be held with these three guys. It was an invaluable experience to many, including ourselves, and we could definitely see ourselves attending for future events, especially as Devil Pad continues to grow to support Hollister, its nearby cities, and the San Francisco Bay Area.